高粘体系分子蒸馏设备是针对高粘度物料(如聚合物添加剂、天然油脂、生物柴油)设计的特种分离装置,通过优化蒸发面结构与热传导机制,实现粘度高达50,000 cP物料的分子级分离。其核心技术突破了传统蒸馏对物料流动性的限制,成为高附加值产品纯化的关键工具。
一、设备核心结构创新
1.刮膜式蒸发器:采用旋转刮刀将物料均匀涂抹为0.1-0.5 mm的液膜,显着提升传热效率。某石化企业通过该技术将聚合物添加剂的分离效率从65%提升至92%,且液膜厚度波动控制在±0.05 mm内,避免局部过热导致的降解。
2.短程冷凝系统:冷凝面与蒸发面间距缩短至0.5-2 mm,确保高粘物料蒸气分子快速冷凝。在鱼油DHA浓缩实验中,该设计使DHA回收率从78%提升至95%,同时减少冷凝器堵塞风险。
3.高真空度维持:配备分子泵与扩散泵组合系统,真空度可达0.001 mbar,使高粘物料沸点降低200-300℃。某生物柴油厂通过该技术将废弃油脂的蒸馏温度从350℃降至120℃,能耗降低40%。
二、高粘体系适应性设计
1.强制循环进料系统:采用齿轮泵与螺旋推进器组合,确保物料以0.1-10 L/min的稳定速率输送。某润滑油再生项目通过该系统将进料波动控制在±2%,避免因流量不稳导致的分离效率下降。
2.耐腐蚀与防粘涂层:蒸发器内壁涂覆碳化硅或聚四氟乙烯涂层,耐温达400℃,且摩擦系数低于0.1。某香料企业通过该涂层将玫瑰精油提取过程中的残留量从15%降至3%,延长设备清洗周期至30天。
3.多级馏分收集:设置3-5级馏分收集器,通过温度梯度(50-250℃)实现粘度差异物料的分段收集。在石蜡油精制中,该技术将轻组分与重组分的纯度分别提升至99.5%和98.8%。
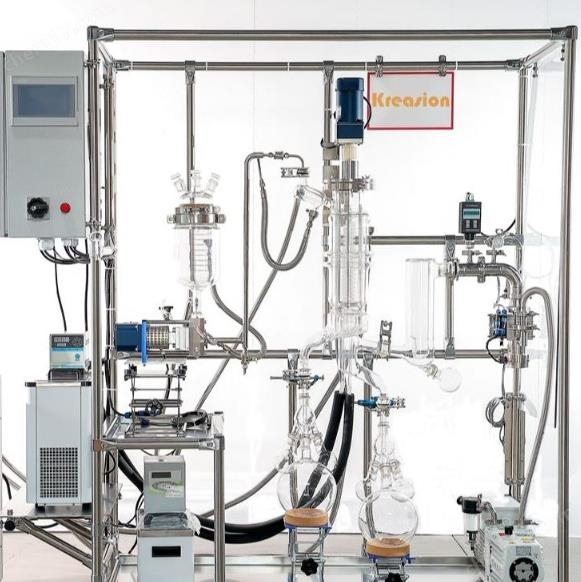
三、应用案例与行业价值
在天然产物提取领域,某企业利用高粘体系分子蒸馏设备从蜂蜡中分离出高纯度三十烷醇(纯度≥99%),产量达50 kg/天,较传统方法提升3倍。在医药中间体合成中,该设备将聚乙二醇的分子量分布系数(PDI)从1.8降至1.2,满足高级制剂要求。
高粘体系分子蒸馏设备通过结构创新与工艺优化,解决了高粘物料分离中的流动性差、易降解、易结焦等难题。未来,随着碳化硅冷凝器、AI动态温控等技术的融合,其处理量将突破1000 L/h,为生物基材料、高级润滑油等领域提供更高效的分离解决方案。